ذغال جوش (هسته امپیدر – Impeder Core) چیست؟
ذغال جوش (هسته امپدر – impeder core) از اجزای اصلی برای تولید لوله و پروفیل می باشد. در واقع ذغال جوش (هسته امپدر – impeder core) به عنوان هسته اصلی برای القای از کویل به عنوان اولیه و پروفیل به عنوان بخش ثانویه در سیستم درز جوش می باشد.
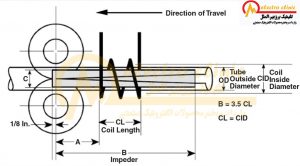
ذغال جوش (هسته امپیدر – Impeder Core) چه کاربردی دارد؟
ذغال جوش (هسته امپیدر – impeder core) شار مغناطیسی ایجاد شده توسط سیم پیچ کار (کویل) را به ناحیه مورد نظر جهت جوش لوله متمرکز می کند. در نتیجه ، استفاده از ذغال جوش (هسته امپیدر – Impeder Core) راندمان فرایند درز جوش را تا حد زیادی افزایش می دهد.
ذغال جوش (هسته امپیدر – impeder core) برای جوش با فرکانس بالا و درز جوش مورد استفاده قرار می گیرد.
اهمیت انتخاب ذغال جوش (هسته امپیدر – Impeder Core)
انتخاب ذغال جوش (هسته امپدر – Impeder Core) مناسب تأثیر قابل توجهی در بهره وری، کیفیت جوش، توان مصرف شده (مصرف انرژی بهتر) و کیفیت درز جوش دارد.
کاشکه ارائه دهنده ذغال جوش برای کاربرد های جوشکاری فرکانس بالا و درز جوش طرای شده با مواد اولیه K 2006
مهمترین ویژگیها در انتخاب ذغال جوش (هسته امپیدر – Impeder Core)
چگالی شار زیاد در ترکیب با دمای بالای کوری (Curie temperature) ، بیشترین نیاز جوشکاری فرکانس بالا (بالاترین توان) را فراهم می کند.
توان تلفاتی پایین هسته در فرکانس بالا باعث عدم افزایش دما هسته می شود در نتیجه باعث افزایش چگالی شار اشباع در محل القا می شود.
چگالی شار بالا در محدوده دما تا 150 درجه سانتی گراد است
توان تلفاتی پایین تلفات کم مصرف در محدوده فرکانس تا 500 کیلوهرتز
نفوذپذیری بالا
ثبات نفوذپذیری در فرکانس بالا تا 1 مگاهرتز
انواع ذغال جوش (هسته امپیدر – Impeder Core)
کاشکه آلمان ارائه دهنده رنج وسیعی از ذغال جوش ( Impeder Core- هسته امپیدر) برای جوشکاری فرکانس بالا می باشد،که میتوان در 5 نوع دسته بندی نمود:
- ذغال جوش شیاردار و سوراخ دار (KRSH)
- ذغال جوش شیاردار (KRS)
- ذغال جوش بدون شیاردار و بدون سوراخ دار (KR)
- ذغال جوش سوراخ دار (KRH)
- ذغال جوش نیمه تخت (KRH)
بستگی به نوع ذغال جوش ( Impeder Core- هسته امپیدر) با قطر 3 الی 95 میلی متر و طول تا 200 میلی متر تولید میگردد.
تولید لوله های درز جوش مستقیم
ابتدا ورق فولادی از کارخانه های فولادساز تهیه میشود تا خطوط تولید لوله به واسطه آن تغذیه گردد از جمله برترین کارخانه های ساخت ورق فولادی می توان به شرکت فولاد مبارکه اصفهان اشاره نمود بعد از آن با توجه به سایز لوله ورق ها در اندازه های مورد نظر برش داده می شوند.
در فاز بعدی ورق های برش خورده از میان غلطک های مخصوص عبور داده شده و لبه های آن به یکدیگر نزدیک می شوند سپس به واسطه دستگاههای جوشی القایی که در خطوط تولید تعبیه شده به یکدیگر متصل می شوند. در این شیوه تولید لوله، در محل اتصال دو لبه ورق، درز جوشی به وجود خواهد آمد بر همین اساس به محصولاتی که به چنین روشی تولید میشوند لوله درزدار یا لوله درز مستقیم گفته می شود.
در شیوه تولیدی مذکور محصولات نهایی اغلب به عنوان مواردی جهت ساخت پروفیل و یا لوله های در اندازه های کوچک تر در مصارف ساختمانی مورد استفاده قرار می گیرند. شیوه دیگر تولید این لوله، برش پس از فرمینگ است در این شیوه مطابق روش قبلی ورق فولادی از میان بخش فورمینگ عبور داده شده جوشکاری شده و سپس خنک می گردد در فاز نهایی از خط سایزینگ عبور داده شده و در اندازه مورد نظر برش داده می شود این محصول بعد از دریافت تاییدیه بازرس مربوطه، بسته بندی و انبار می گردد.
کاربرد انواع لوله درز مستقیم
همان طور که پیش تر نیز ذکر گردید لوله های درز مستقیم یا لوله درز مستقیم جوشی در مصارف صنعتی و ساختمانی کاربرد دارد از جمله عمده مصارف آن میتوان به موارد زیر اشاره نمود:
- استفاده در تاسیسات
- لوله های شوفاژ
- لوله انتقال آب
- لوله انتقال گاز ساخت لوله و پروفیل